Standard Operating Procedures
(SOPS)
A guide to understanding SOPs, how to implement them and some good practice tips and advice from Tom Hughes, CEO of GembaDocs, and lean champion.

Background
Business Leaders often like the idea of having processes documented in order to become less reliant on tribal knowledge which is so easily lost, making business continuity difficult to maintain. Global staff shortages and short term people availability shocks due to issues such as COVID restrictions exacerbate the problem.
However these benefits are only a fraction of what well implemented SOPs can deliver and the fact that these benefits are under-estimated is a significant reason why most businesses are not sufficiently motivated to put living, breathing, useful SOPs in place. They don’t understand the benefits properly, so they don’t allocate the time and resources necessary to make it happen. In addition, up until now current methods to create and maintain SOPs have been super cumbersome, meaning that for most businesses, they don’t see the effort vs reward equation stacking up.
So to understand how this situation can be improved, let’s look at some questions.
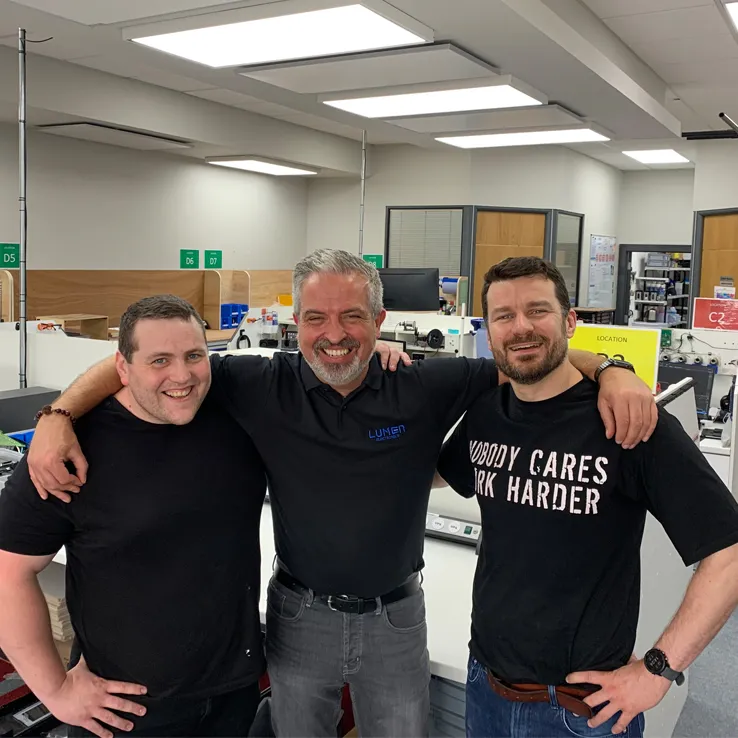
Tom, with the Senior Team at Lumen Electronics
What is an SOP? (Standard Operating Procedure)
“Standard Operating Procedures are detailed descriptions of the prescribed method that team members must follow in order to carry out a given process in a particular organisation.”
Sounds like fun, doesn’t it? 😉
Here is an example of a “step by step” SOP that we generated in our GembaDocs software.
It sounds like we are placing a set of handcuffs on our team members rather than providing a useful tool to help them be more successful in their work.
Therein lies half the problem as to why there are so few successful SOP implementations.
For SOPs to become truly useful in an organisation, the team members need to feel that THEY OWN THEM, not that they have been imposed on them. Nobody likes being a slave. They need to be understood to be tools that make work life easier and better, not milestones around their necks.
The key to doing this well is in our next question.
How to write SOPs
We are very fortunate in that we had a lot of interaction with Mark Warren around the subject of SOPs.
Mark actually WROTE THE MANUAL for how Toyota delivered Standard Work training in North America, called “Training Within Industry.”
He was super kind in helping us understand the principles better. Here is one of the posters we developed from his material because it is so often an area that people get wrong.
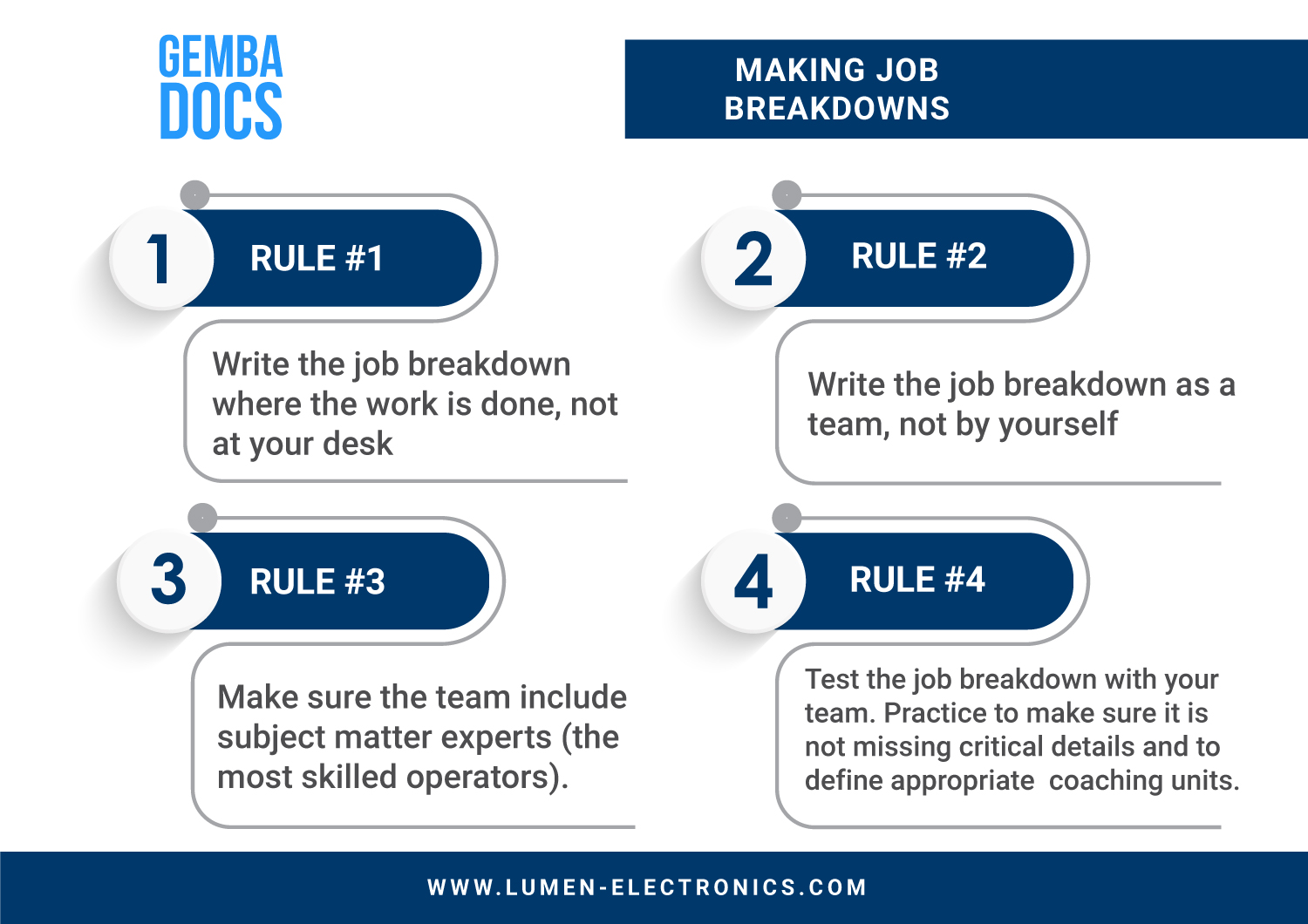
From experience, I know this is important.
During my first ever real job back in automotive, one of my tasks was to write Standard Operating Procedures/Quality Procedures for the ISO9000 manual. It was tremendous because I learned early on, that procedures that looked great on my PC in the office, written by myself were completely useless!
During those early stages, I would proudly take out my shiny new procedure that I’d written with barely any consultation with the guys doing the job and basically get told to move on! (See Rule #1- I’m being very diplomatic in describing what they said)
I learned that the whole process worked much better when I worked with the guys on the workplace/Gemba to document what they were already doing and then work with them to agree any changes that were necessary to meet the Quality Standard. (See Rules #2 & #3 & #4) They had a much higher degree of ownership when I did things that way.
When this is done as a team, each member gets to describe how they carry out the task. Often everyone is doing it differently, and when this is surfaced, everyone gets to contribute and evaluate each other’s method. This leads to what I call the “best of method” where the team agrees on a compilation of each member’s best ways of doing a task, which is better than anyone’s individual approach before. Not only does this create ownership within the team but this process of creating a new baseline raises the standard of how that process is carried out for everyone.
This is a huge source of process improvement, which is one of the most often missed benefits of implementing SOPs. It is also a great way of building team cohesion.
In my early automotive days, I also learned another crucial lesson that few people are truly aware of.
If you are going to create an SOP, if it adds burden to the people doing the job and that burden is not 100% necessary and understood, the standard will definitely not be followed. You will turn yourself into a police person trying to enforce the law all the time. It’s key that the Standard makes getting a high quality outcome easier, not more difficult. Easy, simple, high quality processes get followed. Difficult, complex processes are always a struggle.
How to keep SOPs current/updated/ make sure they are followed?
SOPs can’t be viewed as monuments. By that I mean that once they are put in place, that they are never supposed to be moved! A well implemented SOP culture views SOPs as the baseline, the standard that we all must follow.
However there must also be a process in place that facilitates change and improvement.
This is most often the place that well intentioned SOP efforts fall down.
Outdated methods, such as creating and editing in excel mean that adding or moving a process step turns into hours of effort. As well as managing a proper document control system to cope with revisions.
Often these tasks fall on one over-burdened individual who becomes the bottleneck and eventually people just start to bypass the system. When that happens or if there are other reasons as to why the process to make changes is too cumbersome, it won’t be long before the SOPs just turn into “wallpaper.” By that I mean that they look good, but because they are now out of date, nobody is following them and they probably provide more harm than benefit as they are a false source of security.
This particular pain-point is one of the primary reasons that we developed the GembaDocs software. Edits can be made in seconds, approved in minutes by the appropriate people and put live instantaneously. All done on the Gemba by the appropriate team of people to make and approve the Process Change. No running backwards and forwards to a computer for hours. Minutes.
We don’t know of a better way. It makes SOP’s living, breathing and useful!
Step by step SOPs vs. video SOPs
Some organisations try to deal with SOP’s by using video as a method of documenting a procedure. In the first instance, this seems like the perfect answer. Like it can only take minutes to shoot a video on someone’s phone right?
But then you probably need to edit it, which takes some time.
Then it needs to be hosted somewhere in order to be accessible to people on the Gemba, either on a server, the cloud or a video platform like YouTube or Vimeo.
Still it’s not too bad? Like it’s easy to document our process?
Up until you want to use it as a training tool for a new starter.
For a physical process, we can watch the process together to being with. Then we can pause it intermittently to describe it to the newbie. Now we want to gradually move away from the newbie as they become more autonomous. Are they expected to stop / start the video in order refer to it as they remind themselves of process steps? Not much fun for the newbie.
Now what happens if we want to make a process improvement and the video needs to be revised to bring it up to date?
Where is the video stored? In many organisations that I’ve seen, that’s a good question!
So Video SOP’s make organisations feel good but in order to question how useful they are, ask how many times they get updated? If that number is low, then the SOP is probably either out of date or not much is happening in the way of Process Improvement!
In our organisation, some processes are on revision 10 and they have only been operating for 6 months. We make improvements and update our SOP’s instantaneously on our GembaDocs software.
That’s why we recommend Step by Step SOP’s over video any day. Step by Step SOP’s in general are a better training tool and the lack of friction involved to keep them up to date when making Process Improvements make them a winning solution.
PS – on rare occasions, we integrate short videos into our Step by Step SOP’s for nuanced processes that are tricky to describe in a Step by Step way. We call that a hybrid approach. GembaDocs has a facility to upload a link and display the video as a QR code on the SOP printed document. It’s a rare use case but it happens.
What kind of processes require an SOP?
We have a saying in Lean circles coming from Paul Akers that “everything is a process.” I would add to that by saying that “everything is a process and if it’s a process that it can be documented and it can also be improved!”
So any process can be documented. Here are the two key categories;
1. A core value adding process for an organisation
The “normal” example that people consider here are often around manufacturing processes. It’s true that these kind of SOP’s, especially (Step by Step) originate from that sector. However, that’s not the end of the story. Any business critical process, especially those that are key to adding value for a customer should be documented. An organisation does not have to have a physical product in order for this to be the case. Think of a dentist surgery or a hospital setting for example. There is a process from receiving / registering a patient through to a myriad of different forms of assessment and treatment in the process of this organisation.
So these kinds of processes can be both physical (a manufacturing or distribution process) or virtual / computer-based.
Both will benefit from having an SOP developed to improve Quality, Cost and Consistency of Customer Experience.
2. Simple how to do …….? Turn on a machine / Change a printer cartridge etc.
“Put the answer where the question is!” how many times have we encountered these kinds of interruptions to the flow of our day? How do I change the paper in the printer? How do I access the wifi? How do I book in this client? And on and on. Documenting these “information deficits” on processes that can be significant productivity killers when the knowledge is not there and then making that answer available at point of use is a no-brainer improvement.
How do we make sure SOPs are followed?
When we follow the process for writing the SOP already described, that is a big step towards ensuring that the people actually doing the job feel ownership for the SOP and therefore are likely to follow it but on it’s own this is unlikely to be enough.
It is key that everyone that carries out “task X” is trained in how to do it as per the SOP. This is especially important for business critical, value adding processes.
This was another key part of the learning that we received from Mark.
We developed this graphic based on his material.
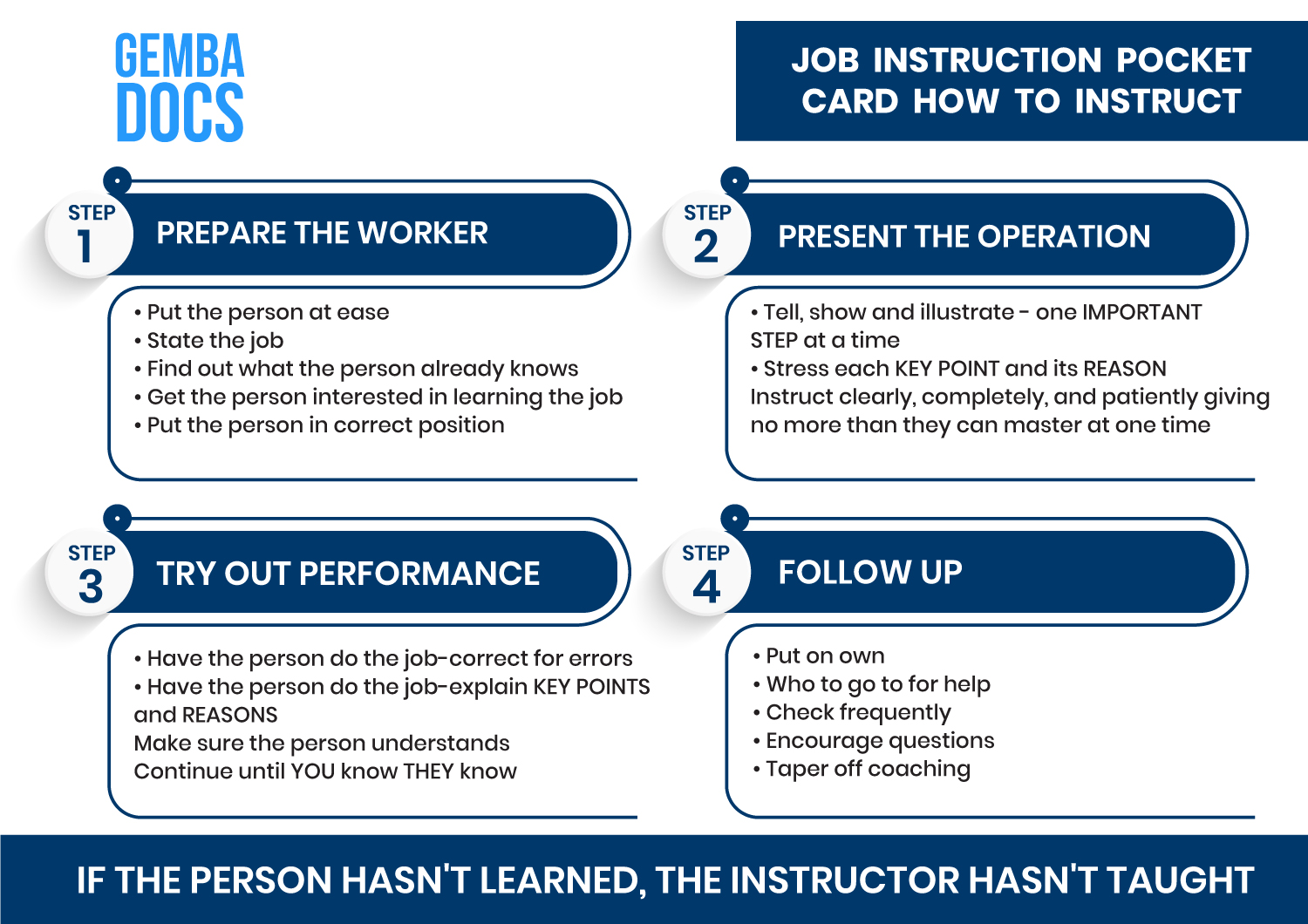
The bottom line of this graphic is the most important. “If the person hasn’t learned, the instructor hasn’t taught.”
In my experience, very few organisations outside of automotive, truly understand this. It’s generally the exact opposite!
So preparing the worker (Step 1) and presenting the operation (Step 2) in a manner that they understand clearly why each step is necessary and the key points to look out for, is the responsibility of the INSTRUCTOR. Trying out the newbie’s performance (Step 3) so that the INSTRUCTOR is validating the understanding and performance of the newbie before they put them on their own (Step 4) and then ensuring that they get adequately supported before tapering off the coaching is key.
For the vast majority of processes, if the newbie doesn’t get it, it is because the process is unclear, too complex or burdensome, or the instructor has not done Steps 1 – 3 properly. It’s a true case of “attack the process, not the person.”
Failure in this area is a key reason why so many businesses have a problem with a “churn” of new starters who do not stay long in the business, whilst creating a huge burden on the long term team members who constantly have to support the new starts, causing further reductions in productivity because they aren’t actually adding value.
It’s a great example, where “pulling the andon” and understanding what the root causes of the problem are really helps. Very often, the problems lie in these areas, poorly documented standards and training processes, that stresses out the new starts and the existing long-term people alike. Management needs to understand this and support a change in approach. The results can be miraculous.
So training is evidently key but it doesn’t just end there.
How to access Standard Operating Procedures?
How team members are able to access the SOP’s is also important. How often have we seen work instructions / how to’s or manuals that are put into a file and then put away in some drawer / cupboard just to gather dust? Hardly a way for them to be living, breathing, useful standards within an organisation!
So no matter what SOP, it’s key that the standard is easily accessible at Point Of Use and that all relevant team members know how to access them.
SOP’s can be made accessible in the following ways;
1. Printed out and displayed in full
2. A QR code which can be scanned by a mobile device to display SOP. This can also be put onto applicable process documentation and automated within an ERP system.
3. A “Lean Bible” where SOP’s can be accessed via url links for reference
4. Via Mobile / Desktop application when they have been generated with specific software e.g. GembaDocs
The appropriate method depends on the application. Incidentally, we designed the GembaDocs software to have “always latest” URL meaning that if they are kept in a Lean Bible or an ERP system, that the URL when clicked / QR code when scanned will always display the latest version of the SOP without the user / administrator needing to do anything else? How cool is that?
Why are SOPs important?
The diagram shows my now favourite Lean quotation of all time from Taiichi Ohno, the “Father of Lean.” “Without standards, there can be no improvement.”
Why would Taiichi make such a bold proclamation?
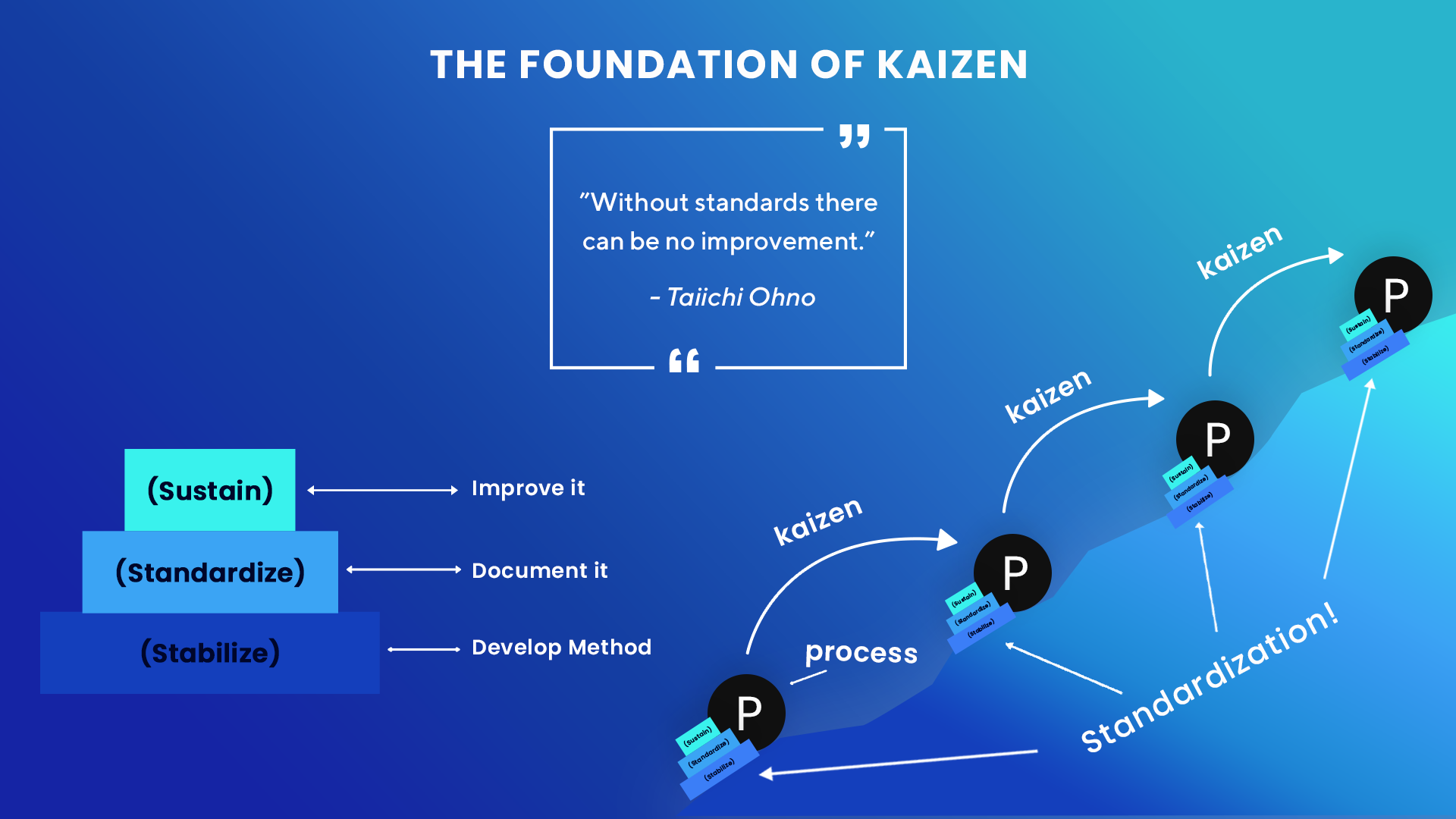
It’s because of that slippery slope between the bottom of the slope shown here, which represents where most companies are, with no standards (SOPs), no documented processes at all or just as bad, what I call “wallpaper” standards that aren’t kept up to date and that nobody is using or following. Still, management that are divorced from the Gemba get to think that they have SOPs in place, when clearly to any objective view that they do not!
We created the GembaDocs software in order to reduce the burden of this Develop – Document - Improve process, making it possible to create or edit Standard Operating Procedures within minutes, not hours or days. It really is a gamechanger making it possible to create and maintain those “backstops” that prevents the solid ball of your process rolling down the Quality, Cost and Customer Experience hill!
This next diagram makes it even more clear that Standards are literally the “foundation of Lean”.
This schematic is often used to demonstrate the Toyota Production System, represented as a “House Of Lean” with Customer Satisfaction and Business Success as the apex of the roof, supported by the pillars of Just In Time, Respect for People (Culture) and Jidoka techniques. The foundation of the temple is “Stability and Standardization” with Standard Operation / Standard Operating Procedures / SOPs as one of those key principles.
It is that important.
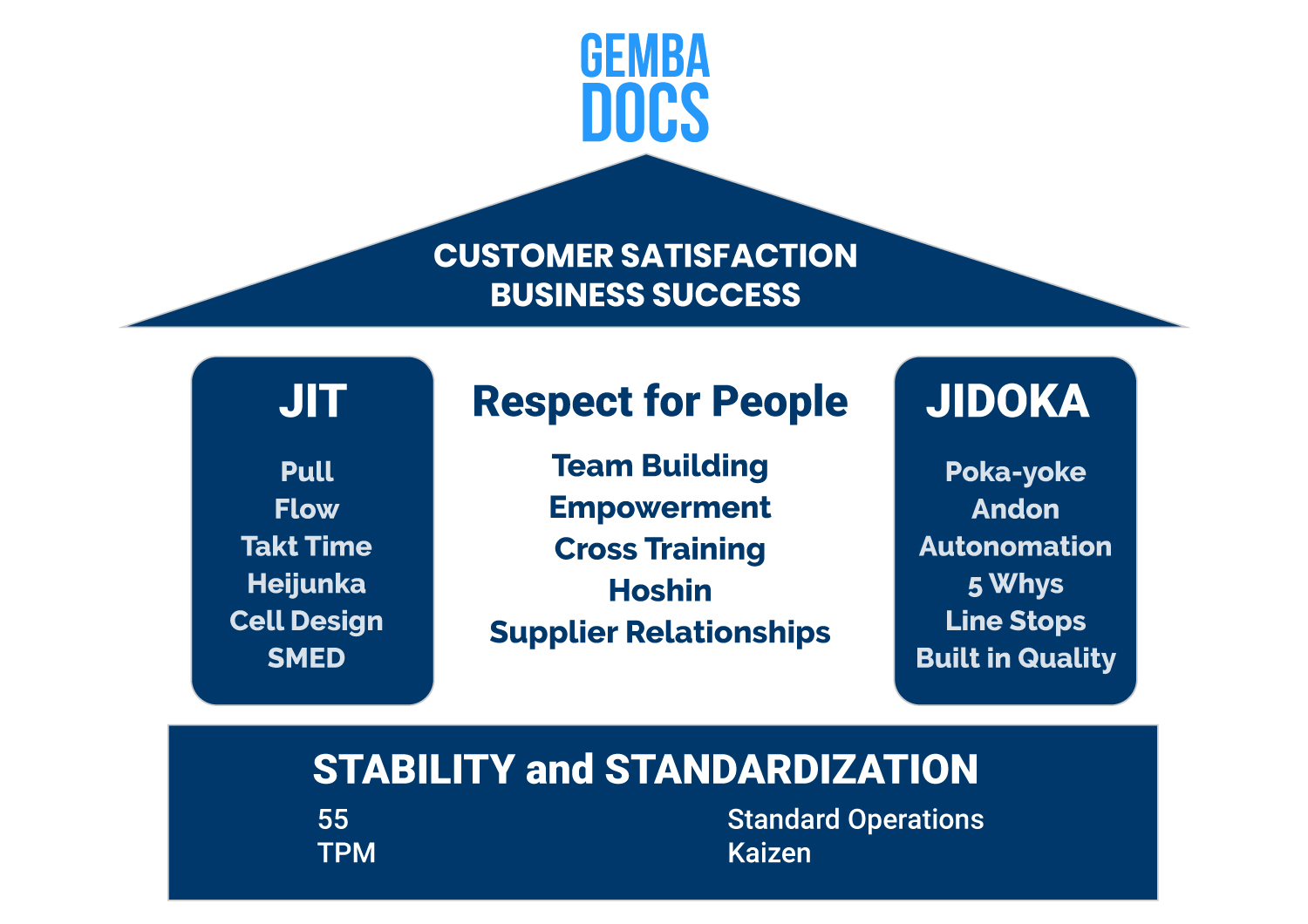
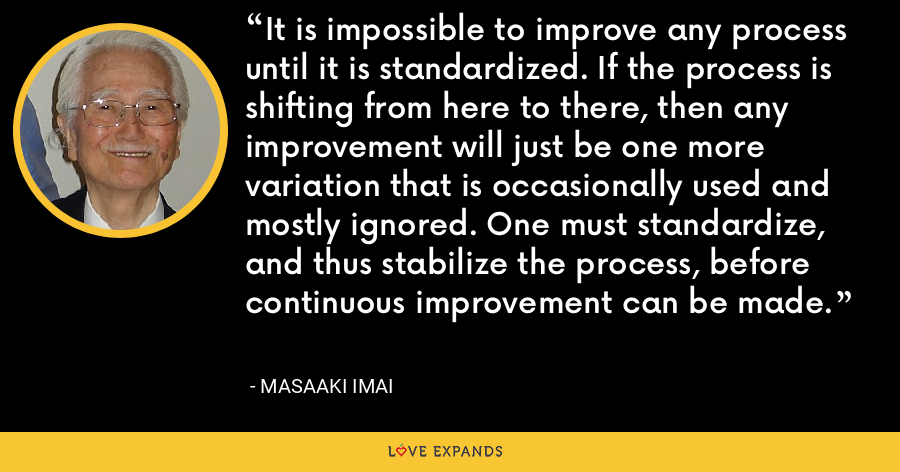
Adding an improvement to that chaos, is just adding another variation that likely will stay in place for a day or two by just some of the people carrying out the process, then disappear.
Lean Guru Masaaki Imai, Founder of the Kaizen Institute describes this phenomenon better than I ever could!
How often have you or your team made a great change to a process, only to come back a few days later to find out that nobody is following it? That can be very frustrating.
That’s why have a clear process of how the Standard Operating Procedures (as we examined in “How to write an SOP”) are documented is key.
5 benefits of standard operating procedures
When we talk about benefits here, we are talking about when SOPs are done right! That can only be achieved when the concept is well understood by all the stakeholders in the organization and the appropriate tools and resources are allocated to the SOP effort.
-
1. A massive source of improvement, the initial “best of” approach becomes the baseline for how process X is done. Secondly, making process improvements on a solid foundation means that they are much more likely to stick than adding another variation to an already unstable process.
-
2. Making process improvements on a solid foundation means that they are much more likely to stick than adding another variation to an already unstable process.
-
3. Reduce stress for team members There is a clear way of executing all tasks for everyone. Minimize planning hassles caused by absentees or people leaving the business. Well implemented SOPs also ensures business continuity.
-
4. Reduce people churn SOPs provide a consistent basis for training. New starts get adequate support to integrate into the organization with the SOPs as their reference.
-
5. Process Stability When team members “own” their already improved process and that SOP is consistently followed by EVERYONE, it leads to less variation in the process outcome, which can often be measured in terms of Quality, Cost or Customer Experience. Overall less waste! We hope that you have received some value from this article. If you would like to discuss more about how SOPs can be applied in your organization, we would love to help.
Platform support: Visit our support hub
General enquiries: Get in touch with us through our form, or email hello@gembadocs.com
Contact us
Support is in UK english